Exploring the Advantages of Injection Molding Factories
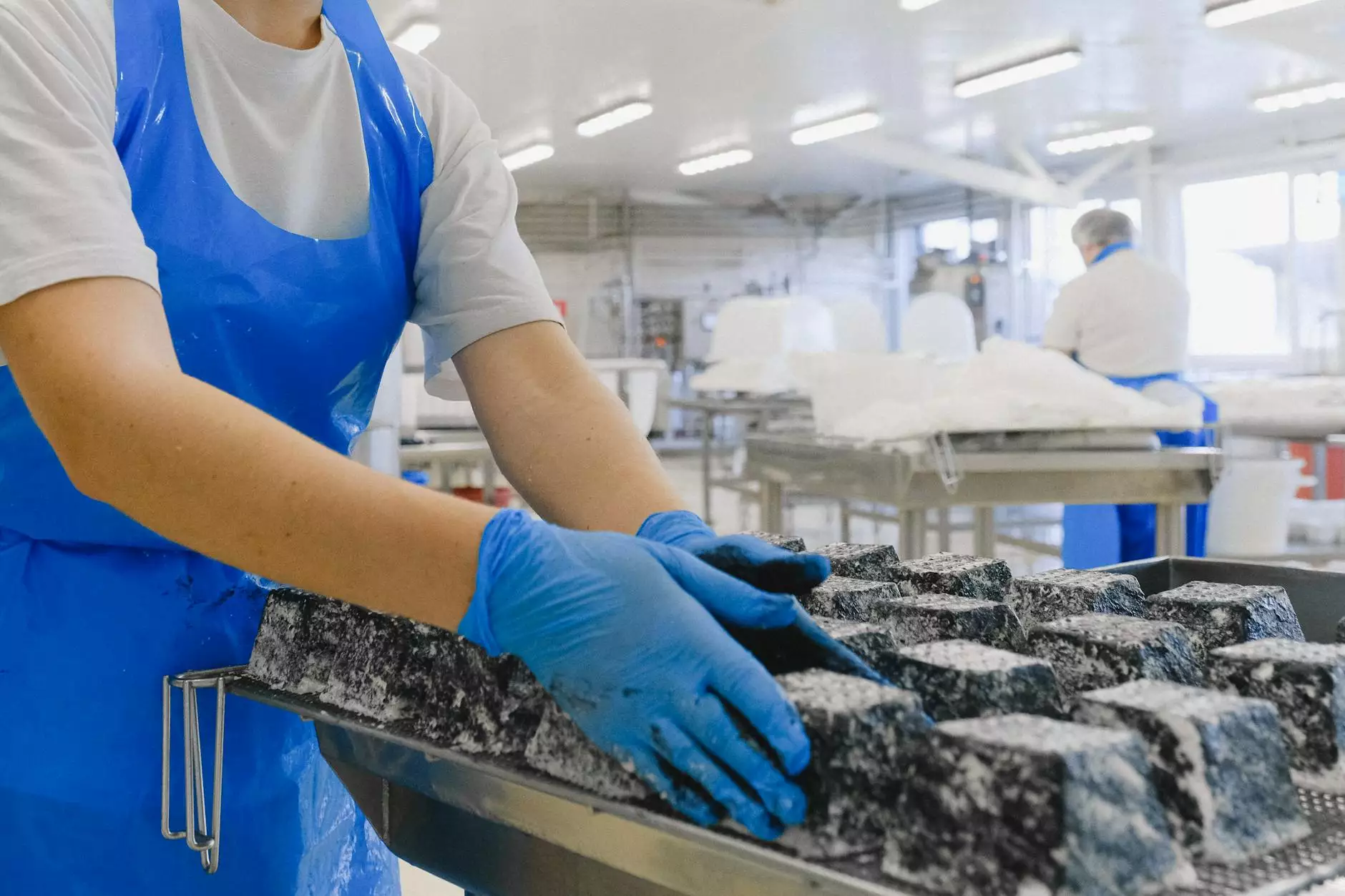
The world of manufacturing has evolved significantly over the past few decades, with injection molding factories taking center stage in the production of intricate and high-quality plastic components. This article delves into the transformative role of injection molding, the benefits it offers, and why it's crucial for businesses in various industries.
Understanding Injection Molding
Injection molding is a manufacturing process where molten plastic is injected into a mold to create specific shapes and designs. This technique is particularly favored for its ability to produce large quantities of consistent and detailed parts in a cost-effective manner. Here’s how it works:
- Material Selection: Different types of thermoplastics and thermosetting plastics can be used, depending on strength, flexibility, and temperature tolerance.
- Mold Creation: Custom molds are designed and fabricated to meet precise specifications for the desired injection-molded product.
- Injection Process: The selected plastic is heated until it becomes molten, then injected into the mold under high pressure.
- Cooling and Ejection: Once the plastic cools and solidifies, the mold opens to eject the finished product.
The Benefits of Using Injection Molding Factories
For businesses considering injection molding as part of their manufacturing process, here are several key advantages:
1. High Efficiency and Speed
One of the most compelling benefits of injection molding factories is their ability to produce items at a rapid pace. Once the mold is prepared, the actual injection process is swift, allowing for:
- Reduced Production Time: Molds can produce parts in seconds, dramatically shortening the overall production cycle.
- High Volume Output: Ideal for mass production, enabling businesses to meet large orders and keep up with demand.
2. Precision and Consistency
Maintaining quality and uniformity in production is crucial for many industries. Injection molding achieves this through:
- High Tolerance Levels: The precision of the mold ensures that each part is consistently produced to exact specifications.
- Minimized Waste: The process is designed to use material efficiently, reducing scrap and material costs.
3. Design Flexibility
Injection molding is not limited to simple designs. It allows for complex geometries, making it possible to create:
- Intricate Shapes: Components that may be difficult or impossible to create using other manufacturing processes.
- Multiple Features: Embedding elements like threads or undercuts directly into the part.
4. Cost-Effectiveness
While the initial investment for molds can be significant, the long-term savings outweigh the costs when producing large quantities. Benefits include:
- Lower Per-Unit Cost: The more parts produced, the lower the cost per item.
- Reduced Labor Costs: Automation in injection molding factories lowers labor needs due to streamlined operations.
5. Material Versatility
Injection molding can accommodate various materials, including:
- Plastics: From commodity plastics to engineered resins, providing options for different performance needs.
- Composites: For parts that require enhanced strength and durability.
Applications of Injection Molding
The versatility of injection molding factories means they cater to numerous sectors, including:
1. Automotive Industry
Injection molding is widely used to produce various automobile parts such as:
- Dashboards
- Body Panels
- Interior Components
2. Consumer Products
Everyday items like containers, bottles, and toys are often produced via injection molding. This method enables:
- Customization: Various colors and finishes can be incorporated into the design.
- Durability: Products made are often long-lasting and withstand everyday use.
3. Electronics
In the electronics field, precision is paramount. Injection molding helps create components like:
- Covers
- Connectors
- Housings
4. Medical Devices
The medical industry relies on injection molding for high-quality, sterile parts such as:
- Syringes
- IV Components
- Diagnostic Equipment
The Future of Injection Molding
As technology progresses, so too does the capabilities of injection molding factories. Several trends indicate the future direction of this manufacturing method:
1. Advanced Materials
New materials, including bioplastics and recycled plastics, are being developed to meet sustainability goals.
2. Smart Manufacturing
The integration of IoT and AI in manufacturing is enhancing efficiency and predictive maintenance, allowing for:
- Real-Time Monitoring: Facilitating quicker response times to production issues.
- Data Analytics: Leveraging insights to optimize production processes.
3. 3D Printing Integration
While injection molding is a dominant method, 3D printing is gaining traction for prototyping and low-volume production, offering:
- Rapid Prototyping: Allowing for quicker design iterations and testing.
- Customization: Easily producing tailored parts based on specific client needs.
Conclusion
The role of injection molding factories in modern manufacturing cannot be overstated. Their efficiency, precision, and adaptability make them indispensable not only in producing high-quality parts but also in driving innovation across various sectors. As industries continue to evolve and demand more sustainable and efficient production methods, injection molding will undoubtedly remain at the forefront, ensuring businesses can meet their growing needs for speed, quality, and customization.
For more information on how injection molding factories can benefit your business, visit deepmould.net.